In the surface treatment process, treater stations utilize high voltage electrodes and ground rolls to generate a corona atmosphere. However, when it comes to selecting the right treater station, there are two primary options to consider: a covered roll or a bare roll treater station. Each has its own set of advantages and disadvantages that must be considered. In this blog post, we will explore the characteristics of both covered roll and bare roll treater stations to help you make an informed decision.
Covered Roll Treater Stations:
Covered roll stations feature a dielectric covering on the ground roll while the high voltage electrode remains bare metal. This configuration offers several benefits:
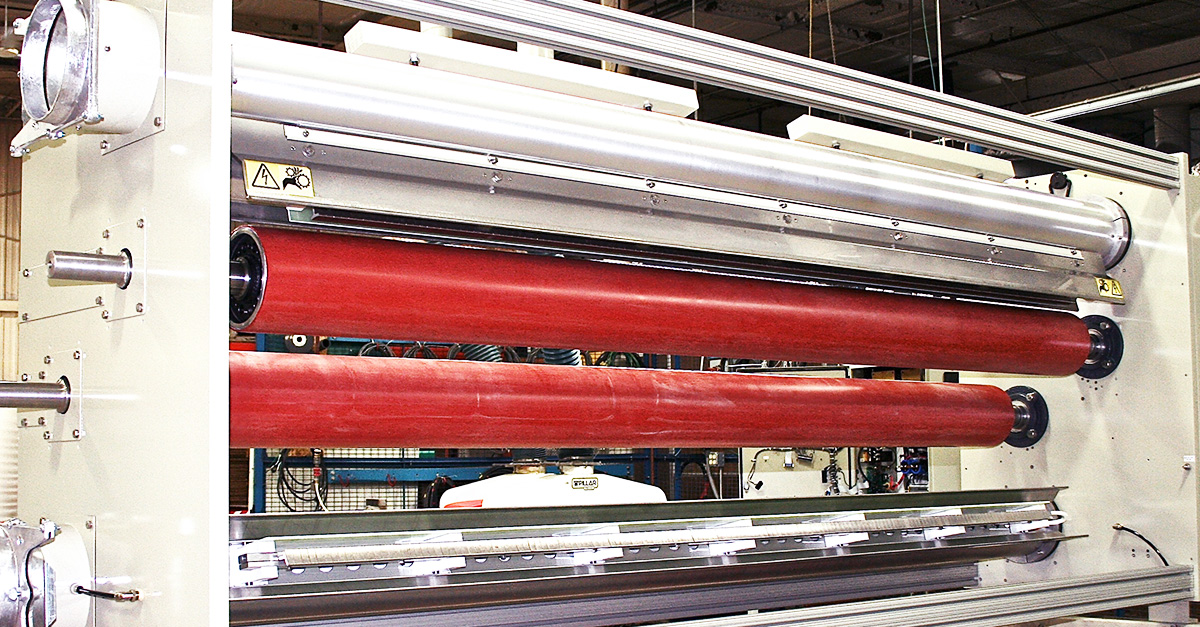
Advantages:
- Ideal for non-conductive surfaces: Covered roll stations are specifically designed to treat non-conductive surfaces more efficiently than a bare roll.
- Effective for difficult substrates: When dealing with challenging substrates such as high slip polypropylene or high slip polyethylene, covered roll stations excel in achieving desired treatment results.
- Adjustable treat width and targeted treatment: These stations allow for easy adjustment of the treat width and enable "lane" treating specific areas while leaving others untreated.
- Versatile dielectric coverings: Various dielectric coverings can be used to accommodate customer preferences for factors like cost, durability, size, and quality.
- Can treat any width material: Covered roll stations have the flexibility to treat materials of varying widths.
Disadvantages:
- Cumbersome repairs: In the event of dielectric failures, repairing covered roll stations can be time-consuming as the roll needs to be completely removed from the station.
- Larger size: Typically, covered roll stations are larger than their bare roll counterparts, requiring more space for installation.
- Inability to treat metallized substrates: Covered roll stations are not suitable for treating metallized substrates due to their design limitations.
Bare Roll Treater Stations:
In contrast to covered roll stations, bare roll treater stations feature a dielectric covering on the high voltage electrode while the ground electrode remains bare metal.
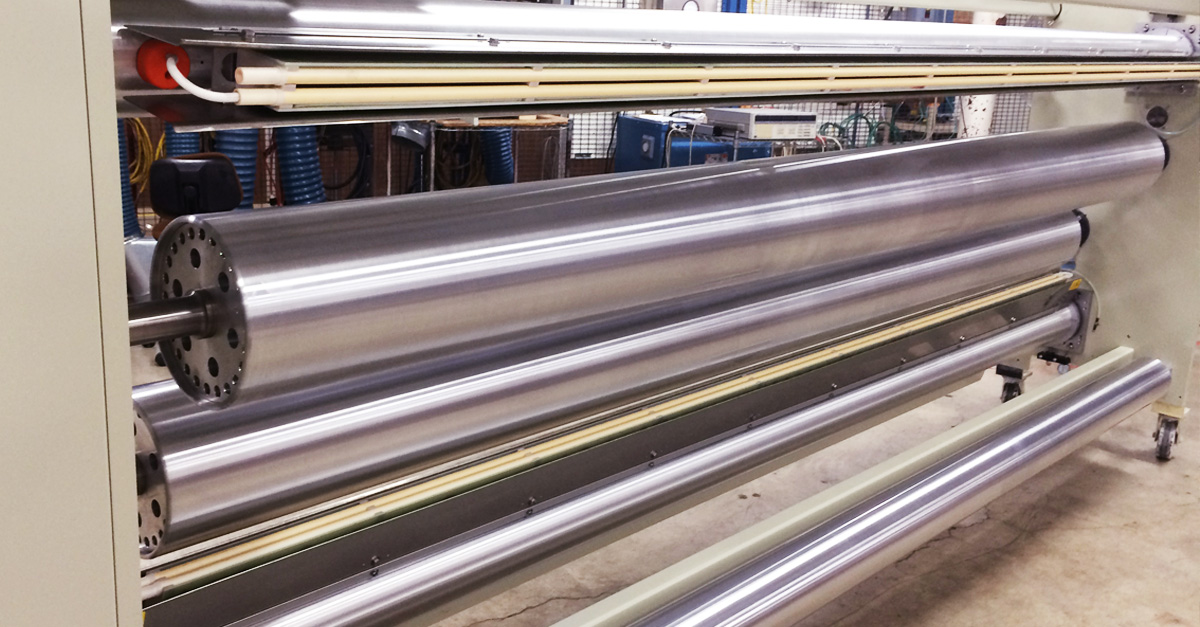
Advantages:
- Metallized substrate compatibility: Bare roll stations have the unique advantage of being able to treat metallized substrates effectively.
- Compact size: These stations are generally more compact in comparison to covered roll stations, making them a space-efficient choice.
- Easy repair of dielectric failures: Bare roll stations allow for easier repairs of dielectric failures on the electrodes.
Disadvantages:
- Lower efficiency: Bare roll stations are considered less efficient than covered roll stations in terms of surface treatment.
- Limited treat width adjustment: Cannot easily adjust the treat width or perform "lane" treatment with bare roll stations.
- Maximum 120-inch treat width: Bare roll stations have a limitation on the maximum treat width, making them unsuitable for wider materials.
- Unsuitability for certain substrates: Certain substrates may not be compatible with bare roll stations, necessitating covered roll treatment methods.
- Cooling requirements: Requires large volumes of makeup air, as air is needed to cool the electrodes.
When it comes to selecting the right treater station, it is essential to consider the specific requirements of your application. Covered roll stations offer advantages in treating non-conductive surfaces, difficult substrates, and allowing for adjustability and customization. On the other hand, bare roll stations are preferable for treating metallized substrates, offer a compact design, and allow for easier repair of dielectric failures. By carefully weighing the advantages and disadvantages outlined in this blog post, you can make an informed decision that aligns with your surface treatment needs.
For additional questions, feel free to contact our technical support team at treaters@pillartech.com.
If you are interested in a treater station for your application, fill out our Request a Quote form today and a Pillar Technologies representative will contact you as soon as possible.