What is Induction Sealing? How does it work?
Induction sealing can be a challenging concept to understand if you're not familiar with the underlying principles. Induction sealing is a non-contact means of heating a metallic disk to hermetically seal the top of plastic and glass containers. The process starts with a multi-layered foil liner, which is spot glued to the inside of the cap or lid of the product. The layers of these liners typically include a backing layer made of cardboard or a paper-like material, the aluminum foil layer which absorbs the electromagnetic energy, and a wax layer that melts during the heating process to help bond the liner to the container. After the liner is placed inside the cap, and the cap is securely screwed onto the container, it is ready to be sealed. With this, proper torque is essential to ensure a tight fit which is necessary for achieving an effective seal during the induction process.
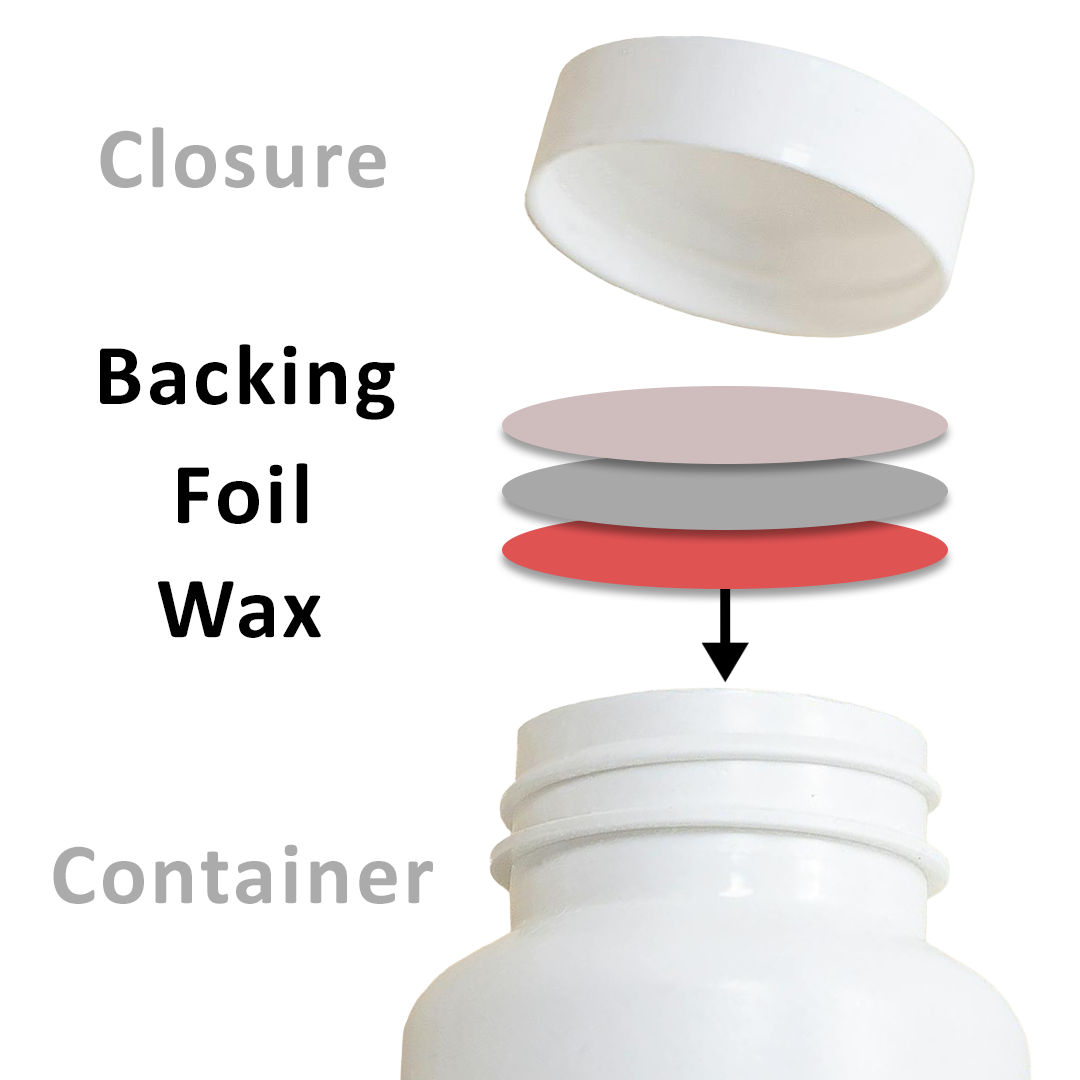
To begin sealing, the container must first pass under the induction sealing coil, where the induction heating process takes place. Induction heating is a phenomenon where electrical energy is transferred to a conductive material, such as foil, by means of an electromagnetic field.
When the container passes under the coil, the induction coil generates an electromagnetic field. This induces eddy currents in the aluminum foil liner of the container's cap. These eddy currents generate heat through electrical resistance, causing the foil to heat up. As the foil heats up, it melts the wax layer, bonding the foil to the container's opening. The cardboard backing of the liner separates and remains inside of the cap. As the product leaves the induction sealer and the heat seal cools, the foil firmly adheres to the container, creating a strong and reliable seal.
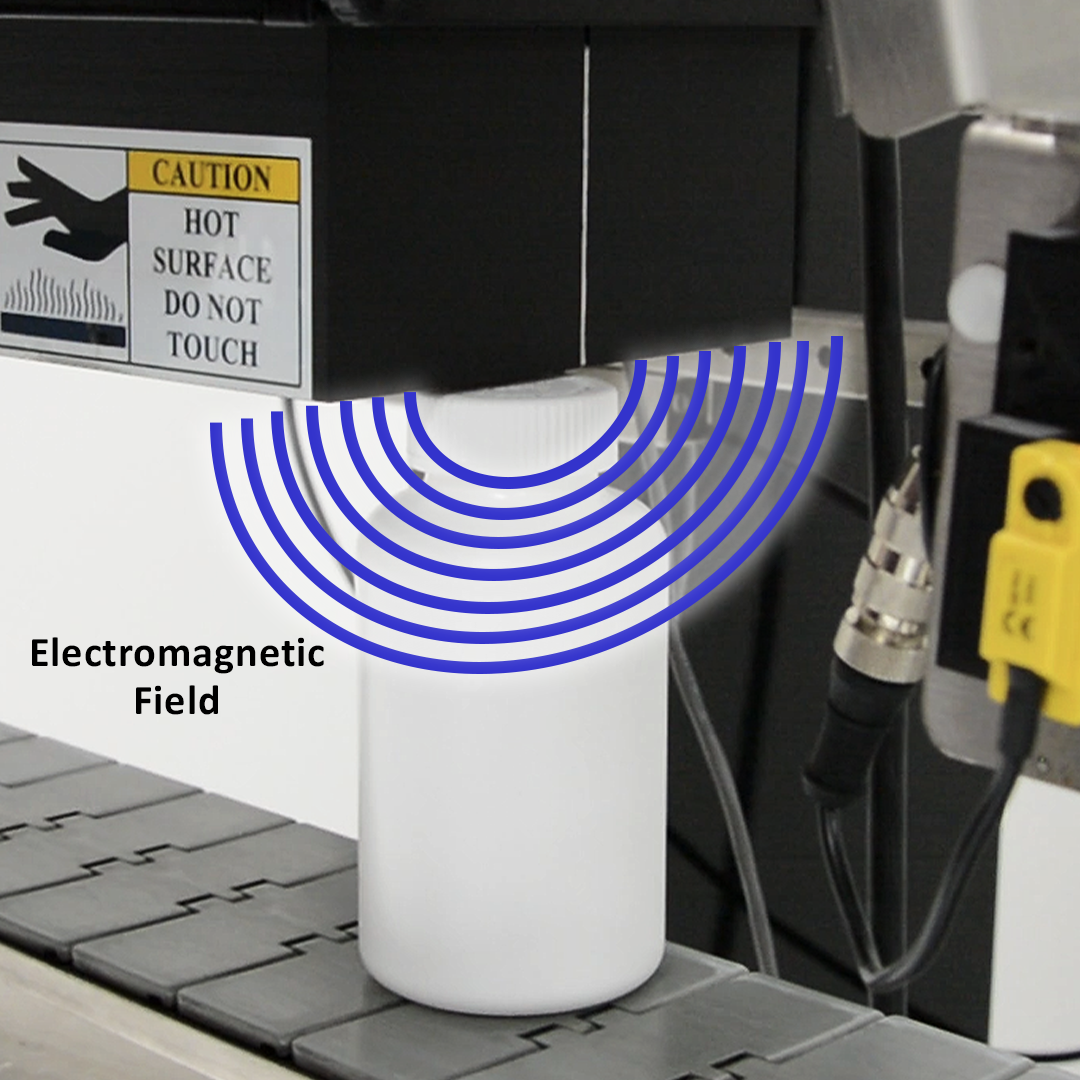
Why is Induction Sealing Important?
Induction sealing is crucial for many industries that are sealing plastic bottles and containers for packaging products, such as pharmaceuticals, health and beauty products, chemicals, and automotive. Induction sealing helps to prevent leaks by creating an airtight seal that keeps products secure in their containers, while keeping everything else out. The inner seal of induction sealed containers acts as a barrier that locks in freshness to preserve aroma and flavor - helping to keep products as fresh as the day you sealed them. Manufacturers also rely on induction sealing to protect against pilferage and provide tamper evidence to customers. Containers that have been induction sealed protect against people trying to break in and tamper with products, and also provides tamper evidence by making unauthorized access to a product or container easily detectable by customers.
How can Pillar Technologies Help?
Pillar Technologies is recognized globally as a worldwide manufacturer of high efficiency induction sealing solutions. With over 50 years of experience serving the packaging industry, Pillar is the ultimate resource for all of your induction sealing needs. Not only is Pillar the preferred supplier of Global 100 brand owners, but it is the only supplier of powerful sealing systems up to 6 kW for the highest speed sealing applications. Pillar induction sealers have been engineered down to fine detail for the most efficient, reliable, and high-quality sealing applications in the industry. Built on flexibility and interchangeability, Pillar's induction sealing solutions help to reduce customer operating costs, eliminate downtime from changeovers, and further reduce the ownership costs of induction sealing operations.
To learn more about Pillar Technologies' induction sealing solutions, or how the induction sealing process works, feel free to contact us or email us at sealers@pillartech.com.